
Timeless pottery loved by enthusiasts for more than 400 years, Karatsu ware got its start in Kitahata.
There is a saying used by Sen no Rikyu and other tea masters regarding the ranking of tea ware: "First Ido, Second Raku, Third Karatsu". For purely Japanese wares the saying is slightly different: "First Raku, Second Hagi, Third Karatsu", however in both cases Karatsu ware is among the top 3 wares for tea.
Conventional knowledge tells us that Karatsu ware got its start with the invasion of the Korean Peninsula by Toyotomi Hideyoshi from 1592 -1598, after Korean potters returning with the Japanese army started producing ceramics. However, even prior to this it is said that Sen no Rikyu treasured Karatsu ware. Based on the fact that Karatsu ware dated to 1592 exists in Iki, Nagasaki, at Shoumogu, it is estimated that by the 1580's the production of Karatsu ware had already begun.
Kishidake, the birthplace of Karatsu ware, is located in Kitahata. More than 400 years ago, a powerful seafaring clan, the Hata Clan, held a castle and ruled over the region surrounding Kishidake. They invited potters from the Korean peninsula and China and built kilns, a venture likely made possible by their trade route connections.
Karatsu ware's unique texture and feeling comes from the native clay
Why did the potters of time choose to build their kilns in Kitahata? Because the clay around Kishidake is derived from feldspathic sandstone, which allows it to vitrify at high temperatures, resulting in a hard, impermeable clay body which at the same time possesses a unique rough, rustic texture.
The Korean potters searched the landscape for the ideal clay, and settled
in the foothills of Kishidake. Here they built kilns and passed along their
knowledge of ceramics to the Japanese. Of particular importance was the
creation of the first kickwheels and climbing kilns in Japan, allowing
for efficient increased production of high quality ceramic wares. The fortunes
of Karatsu ware continued to rise hand in hand with the trends of the tea
ceremony, and the production of Karatsu ware spread to the surrounding
countryside, and much ware was exported from the port of Karatsu. In this
way, pottery in western Japan came to be known as Karatsumono, just as
in eastern Japan it came to be known as Setomono.
The revival of Karatsu ware
Compared to pottery produced up to that time in Japan, Karatsu ware was fresh and new, featuring glazes and decoration never before seen. Brush decoration, including that of grasses and trees, featured simple, dynamic lines, and is said to be the first example of brush decorated ware in Japan.
In addition, ash glazes, iron glazes, and rice straw ash glazes resulted in Chosen Karatsu, Madara Karatsu, and Kuro Karatsu wares. The use of white slip for inlay, brushing, and dipping resulted in Mishima and Kohiki wares.
However, at the beginning of the Edo period, the Nabeshima Clan came to power and exerted their influence towards producing porcelain in Arita and Imari. Karatsu ware continued to be produced as tribute to the Emperor, but the kilns dwindled and finally came to be consolidated into the Goyogama near Karatsu castle.
「絵唐津」Brush Decorated Karatsu (E-Karatsu)(Private Collection · Momoyama ~Edo Early)
「無地唐津」Undecorated Karatsu (Muji Karatsu)(Private Collection · Momoyama ~Edo Early)
「沓型茶碗」「Kotsugata Chawan」( Private Collection · Momoyama ~Edo Early)
「水指」「Mizusashi」( Private Collection · Momoyama ~Edo Early)
「花入れ」「Hanaire」( Private Collection · Momoyama ~Edo Early)
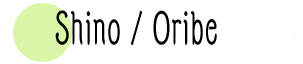
There are many similarities between Karatsu and Mino ceramics.
The influence of Shino and Oribe ware can be seen in the shapes and decoration motifs of Karatsu ware. With its similarites in color and surface, ware known as Mino Karatsu attests to this close relationship.
It is believed that the master/apprentice relationship between Mino's domain lord Tsumagi and Karatsu's domain lord Terasawa made a range of technical exchange possible.
It is said that the Karatsu kilns were used as reference for the construction of the Mino climbing kilns. Conversely, fragments of Mino kilns have been excavated from kiln sites on the north side of Kishidake.
Many Shino and Oribe pottery fragments have been excavated from Karatsu area castle ruins.
Furuta Oribe is generally recognized as responsible for the Oribe style
of ceramic ware. Here, Furuta Oribe is shown traveling by ship with the
Hata family to the Korean Peninsula in search of a climbing kiln, in the
comic "Heugemono", in which Furuta Oribe is the main character.
彫唐津茶碗「Horikaratsu Chawan」
織部格子文沓茶碗「Oribe Koushi Kutsugata Chawan」

- Taken from "About Karatsu ware", from Saga University's 「Hito/Monozukuri Karatsu Project」. -
One characteristic of Karatsu ware is the importance placed on the materials for producing it.
Materials are collected from the potter's locale, rocks are crushed and levigated, then blended and wedged into a clay body; local plants are burned for ash to be made into glazes.
Potters take care in the forming, decorating, and glazing stages to bring out the natural beauty of the materials. Building one's own climbing kiln and firing with wood is considered standard.
Using old Karatsu ware as a model, and using local materials, potters create works that are innately unique and possessing of a character unseen in modern mass produced wares.

1.Clay body
Much of Karatsu ware's appeal comes from the clay body. Each of the old
Karatsu kilns had characteristic forms and clay surfaces, indicating the width
and breadth of materials utilized.
※Tsuchimise: Areas of bare clay on a piece of pottery. The bare foot of
Karatsu ware is considered the standard a point of particular importance.
2.Wheel
※Wheel (Rokuro)
Composed of a flywheel, axial rod, and wheel head, old style pottery wheels
are powered by the potter via hands or feet. Modern electric wheels are now
common, however Karatsu potters commonly use a kickwheel, powered by
either treading or kicking the flywheel.
※The coil and paddle technique
Larger vases and jars are produced by stacking coils of clay which are then
paddled repeatedly with a paddle on the outside of the pot and an anvil on the interior, a process which compresses and strengthens the vessel wall.
3.Trimming
Trimming when the clay is still soft to reveal its natural texture.
4.Bisqueing
Ware is sometimes bisque fired to about 800 degrees celsius, to make it more durable for decoration and glazing.
5.Brush decoration
Iron pigment used for brush decoration fires to black or brown in the finished ware.
6.Glazes
Glazes are applied to raw or bisqued ware using a variety of techniques.
7.Loading the Kiln
Ware is loaded piece by piece into the kiln and potters each have their own kiln
loading preferences. Loading is a particularly important step in the firing
process and determining the final character of a piece.
8.Firing
Heating the ware in a wood, gas, or electric kiln to temperatures of
1250 – 1300 degrees celsius.
The firing technique greatly influences the final color of the ware.
※Climbing Kiln
One type of wood fueled kiln constructed on an incline.
Climbing kilns come in many sizes and configurations, but are generally fuel
efficient and suited to mass production.
Introduced to Japan at the end of the 16th century, they quickly became the
predominant style of kiln, and are capable of reaching temperatures in
excess of 1300 degrees celsius.

Brush Decorated Karatsu (E-Karatsu)
Iron pigment designs are applied by brush to a relatively low iron clay body, then an ash or feldspar based clear glaze is applied. The iron pigment is derived from local high iron clays and minerals, and is applied in simple, abstract designs, resulting in ware with a rustic, warm atmosphere. Common motifs are plants, animals, lines, and geometric patterns in which the influence of Korean ceramics and Mino's Shino and Oribe ceramics (Gifu Prefecture) can be seen.
Undecorated Karatsu (Muji Karatsu)
Ware that has been glazed with just one clear or milky glaze is referred to as “mujimono”.
It is the simplest example of Karatsu ware, most commonly glazed with a simple ash or feldspar based clear glaze.
Mottled Karatsu (Madara Karatsu)
Rice straw ash is the main ingredient in this opaque, milky glaze which was first seen in Japan in the Old Karatsu kilns of the 16th century. The glaze, iron in the clay body, clay texture, and pine ash from the kiln fuel all interact to produce a mottled surface ranging from clear to creamy white with a range of blue to black mottling. There are many teabowls and small cups in this style.
※Old Karatsu Kilns
There are over 200 known kiln ruins, not only within Karatsu city, but throughout Imari, Arita, Takeo, Taku, Ureshino, as well as into Nagasaki prefecture.
Green / Yellow Karatsu
(Ao Karatsu / Ki Karatsu)
Karatsu ware in which an ash glaze has been applied. The iron in the glaze reacts in the kiln atmosphere, turning green in a reduction atmosphere and yellow in an oxidation atmosphere. Ash glaze has a lower melting point, and tends to flow on the ware, creating deep blues where it pools.
※OF(Oxidation Flame)
Kiln flame with sufficient oxygen supplied to produce complete combustion.
※RF(Reduction Flame)
Kiln flame with an insufficient oxygen supply, resulting in incomplete
combustion. This type of oxygen starved flame will seek extra oxygen molecules
from glazes and clay body of the ware itself, resulting in color changes.
Chosen Karatsu (Chosen Karatsu)
Ware that has been glazed with both a high iron ash glaze and a rice straw ash glaze, applied separately top/bottom or left/right on the ware. The contrast of the white and brown glazes creates a multihued waterfall effect of white, blue, and yellow where the glazes melt together and flow. There are many Chosen Karatsu water containers, flower vases, flasks, etc... used as tea ceremony implements.
※Landscape and patina (Keshiki)
Words used to describe the natural, unpredictable changes to the surface of the ware. The various expressions of the bare clay are called “tsuchiaji” (lit. clay flavor). The patina of changes in the ware surface through use is highly prized in the tea ceremony. The fine tearing in the clay of the soft trimmed foot, resembling satin crepe fabric is called “chirimenjiwa” (lit. crepe wrinkles), and the soft fine crawling of the glaze is called “kairagi” (lit. plum bark ) because it resembles the rough bark of a plum tree.
Black Karatsu (Kuro Karatsu)
Ware with a black glaze applied. Iron bearing clay and/or stones are powdered and added to an ash glaze, resulting in colors ranging from honey to dark black, depending on the amount of iron. Iron bearing slips are another technique for achieving a black surface.
Iron content and oxygen levels result in colors ranging from brown to rust to black, and are all referred to as Black (Kuro) Karatsu
※Other types of ware
The classification of Karatsu ware is not exact, and there are many other types not listed above. White slip brushing techniques include Hakeme Karatsu and Kushime Karatsu, carving the clay surface is called Hori Karatsu, overlapping green and brown glazes is called Nisai Karatsu, and scaly glaze surfaces are called Jakatsu Karatsu.
Mishima Karatsu / Kohiki
Mishima Karatsu is the Japanese term for the Korean Funseishaki ware. White slip is applied as decoration using various techniques.
In Japan, this treatment is often seen on tea bowls and other tea implements, and is produced in many regions. The Old Karatsu kilns started producing this ware during the Edo period, and brushed white slip ware is called Mishima. White slip dipped ware is called Kohiki, and was not produced by the old kilns, but rather a comparatively new technique in the Karatsu area.

Handling Karatsu Ware
1.Developing the Patina
In the surface of most Karatsu ware there is a fine crackle from which
water may penetrate. With use, tea tannins penetrate with the water creating
color changes in the ware, resulting in a one of a kind vessel. If you
wish to slow down or prevent this patina development, soak your ware in
clean water before using.
2.Be gentle
Karatsu ware may chip and crack if it bumps into other hard objects such as metal or porcelain ware. It is best to keep them separate for washing. Finely made Karatsu ware is not suited for dishwashers. After hand washing, dry carefully and store. Proper washing and drying will prevent mold and other stains.
3.If the ware perspires
Karatsu ware will sometimes perspire if left full of liquid for long periods. This is a characteristic of the rough Karatsu clay. This perspiration stops gradually with repeated use.

Kishidake Group Kiln Ruins
The Kishidake Group Kiln Ruins were designated as a National Historic Ruin Site in 2005
It is widely believed that domain lord of the Kishidake region, Lord Hata, invited Korean potters and built the kilns of the Kishidake group prior to the Bunroku・Keicho period (1592 – 1598), and as early as the 1580's. For this reason, the Kishidake group kiln ruins are recognized as the oldest climbing kilns in Japan, and in 2005 are designated a National Historic Ruin Site.